How Windscreens Are Made: A Comprehensive Guide
Windscreens, or windshields, are crucial components of any vehicle, providing essential safety and visibility. The manufacturing process of windscreens involves advanced technology and precise methods to ensure they can withstand various stresses while offering clear, unobstructed vision.
True Value Windscreens is dedicated to delivering high-quality windscreen solutions, and understanding how these components are made can help you appreciate the craftsmanship and precision involved in their creation. This article delves into the intricate process of windscreen manufacturing, explaining the materials, steps, and technology used to create these vital automotive components.

The Raw Materials for a Strong Windscreen
The production of windscreens begins with a blend of raw materials that are carefully selected and mixed to achieve the desired properties. These primary components include silica sand, soda ash, and limestone, each contributing to the windscreen's strength and clarity.
Silica Sand: Silica sand is the cornerstone of the glass-making process, forming approximately 70% of the total mixture. Its high silicon dioxide content provides the primary structural framework for the glass, contributing to its strength and clarity. The purity of silica sand is crucial, as impurities can compromise the quality of the glass. Additionally, silica sand’s ability to withstand the extreme temperatures involved in the melting process ensures that it integrates seamlessly into the molten glass without degrading. This makes silica sand an indispensable component in creating high-quality, durable glass.
Soda Ash: Soda ash, or sodium carbonate, comprises about 15% of the glass mixture and plays a vital role as a flux. By lowering the melting point of silica sand, soda ash facilitates the fusion of the sand into glass at lower temperatures, which is both energy-efficient and cost-effective. This reduction in melting temperature helps minimize energy consumption during production, making the process more environmentally friendly. Additionally, soda ash contributes to the glass's smoothness and clarity by reducing the viscosity of the molten material, ensuring a consistent and high-quality final product.
Limestone: Limestone, or calcium carbonate, contributes around 10% to the glass composition and is essential for stabilizing the glass. It enhances the glass’s durability by improving its resistance to weathering and chemical attacks, ensuring longevity and performance under various environmental conditions. The presence of limestone also helps in controlling the glass’s thermal expansion, preventing it from cracking under temperature fluctuations. By fortifying the glass against environmental stresses, limestone ensures that the windscreen maintains its integrity and functionality over time.
Other Additives: To further enhance the glass’s properties, various other additives are incorporated into the mixture, accounting for approximately 5% of the total composition. Additives like alumina and magnesium oxide are crucial for increasing the glass’s resistance to thermal shock and mechanical stress. These materials improve the glass’s overall strength and durability, allowing it to withstand extreme conditions and impacts. By fine-tuning the glass’s performance characteristics, these additives ensure that the final product meets rigorous safety and quality standards.
Melting and Forming the Glass
Once the raw materials are prepared, they are mixed and melted to form the basic glass. This stage involves several critical steps to ensure the glass achieves the necessary quality and characteristics.
Batch Mixing: Batch mixing is the foundational step in the windscreen manufacturing process, where raw materials are meticulously combined in precise proportions. This ensures that the resulting mixture has a uniform composition, which is crucial for producing high-quality glass. The carefully mixed batch is then transferred to a furnace, where it is subjected to extremely high temperatures ranging from 1,600 to 1,700 degrees Celsius. This intense heat causes the raw materials to melt and blend, forming a molten glass with the desired properties. Achieving the correct temperature and blending is essential to ensure the glass has the strength and clarity needed for use in windscreens.
Melting Process: The melting process involves heating the mixed raw materials in a furnace to transform them into molten glass. Maintaining a consistent temperature within the furnace is critical to ensure that the glass melts evenly and does not develop imperfections. During this stage, it is essential to eliminate any bubbles or impurities from the molten glass, as these can affect the final product’s clarity and strength. The furnace used for this process may be powered by electricity or gas, depending on the specific setup of the manufacturing facility. Ensuring a bubble-free and pure molten glass is crucial for producing high-quality windscreens that meet safety standards.
Forming the Glass: Once the glass has melted, it is shaped into its final form through various techniques. One common method used is the float glass process, where the molten glass is poured onto a bed of molten tin, allowing it to spread evenly and form a flat, smooth surface. This technique ensures that the glass has a uniform thickness and an impeccable surface finish. For windscreens with curved shapes, the glass is heated until it becomes pliable and then pressed into a mold to achieve the desired curvature. This process requires precise control of temperature and pressure to ensure that the final product fits perfectly within the vehicle’s frame and provides optimal visibility.
Tempering and Curving the Glass
To meet stringent safety standards, laminated glass undergoes rigorous tempering and curving processes to enhance its strength and shape. The tempering process involves heating the glass to extremely high temperatures and then rapidly cooling it, a technique known as thermal tempering. This procedure creates compressive stresses on the glass surface, significantly improving its resistance to impacts and thermal stress, thus making it highly suitable for automotive applications.
For windscreens requiring curved shapes, the glass is first heated until it becomes pliable and then shaped using precise molds. This controlled process ensures that the curvature is uniform and that the glass fits seamlessly within the vehicle's frame. After the tempering and curving processes, the windscreen undergoes a thorough inspection to verify its uniformity and accuracy, with any deviations from the required specifications being corrected to ensure a perfect fit and optimal performance.
Enhanced Mobile Repair Solutions
Choosing the right windscreen washer fluid is essential for effective cleaning and de-icing. Standard all-season washer fluids often freeze in cold temperatures, which can impair their function and potentially damage the washer system. Winter-specific washer fluids are formulated to remain liquid at much lower temperatures and often contain de-icing agents to prevent frost build-up. Regularly refilling your washer fluid with a winter blend ensures that your system operates effectively, helping to maintain clear visibility despite icy conditions.
Water-repellent and de-icing washer fluids offer additional benefits by preventing the build-up of frost and ice. These fluids use advanced technology to create a protective layer on your windscreen, enhancing water dispersion and reducing the need for frequent cleaning. By using high-quality winter washer fluids, you ensure that your windscreen remains clean and clear, improving your driving experience and safety during the colder months.
Installing Additional Features
Modern windscreens are often equipped with advanced features that significantly enhance their functionality and user experience. For instance, many windscreens come with embedded heating elements designed to quickly defrost the glass and improve visibility during cold weather. These elements are typically composed of thin metallic wires or conductive films, which effectively distribute heat across the surface. Additionally, some windscreens include tinting and UV protection to reduce glare and shield occupants from harmful ultraviolet rays.
Tinting is achieved by incorporating colored additives during the manufacturing process, while UV protection is applied through a special coating. Moreover, high-tech windscreens may integrate sensors and cameras that support various functions such as lane departure warnings and automatic braking systems. These components are meticulously installed and calibrated during production to ensure optimal performance and safety.
Final Assembly and Quality Checks
The final stages of windscreen production involve assembling and inspecting the finished product to ensure it meets all safety and quality standards.
Cutting and Shaping: After the glass has been laminated and tempered, it is meticulously cut to the precise dimensions required for vehicle installation. This step uses advanced cutting tools, such as diamond-edged saws and water jets, to ensure that the edges are smooth and the sizing is accurate. The precision in cutting is crucial to ensure a perfect fit within the vehicle frame, which is essential for both the functionality and safety of the windscreen. Any inaccuracies at this stage could lead to installation issues or compromise the windscreen’s performance.
Final Inspection:
Once the cutting and shaping are complete, each windscreen undergoes a thorough final inspection to ensure it meets all quality standards. Inspectors check for any visible defects such as bubbles, cracks, or distortions in the glass, as well as verify the clarity and overall finish. This stage also involves testing any additional features, such as heating elements or sensors, to ensure they are correctly integrated and functional. The goal is to ensure that the windscreen not only looks flawless but also performs reliably under various conditions.
Packaging and Shipping: After passing the final inspection, the windscreen is carefully packaged to safeguard it during transportation. Specialized packaging materials, such as cushioned wraps and reinforced cartons, are used to protect the glass from impacts and environmental damage. The packaging is designed to keep the windscreen secure and prevent any movement that could cause damage during transit. This careful handling ensures that the windscreen arrives at its destination in pristine condition, ready for installation.
Final Thoughts
Understanding the process of how windscreens are made highlights the complexity and precision involved in creating these essential automotive components. From the careful selection of raw materials to the intricate processes of melting, forming, and laminating, every step is designed to ensure that the windscreen provides optimal safety and performance.
For all your windscreen needs, including repairs and replacements, consider reaching out to
True Value Windscreens. Their commitment to quality and customer satisfaction ensures that you receive the best possible service, whether you’re dealing with a minor chip or a complete windscreen replacement. By choosing True Value Windscreens, you ensure that your vehicle is equipped with top-quality windscreens that meet the highest safety standards.
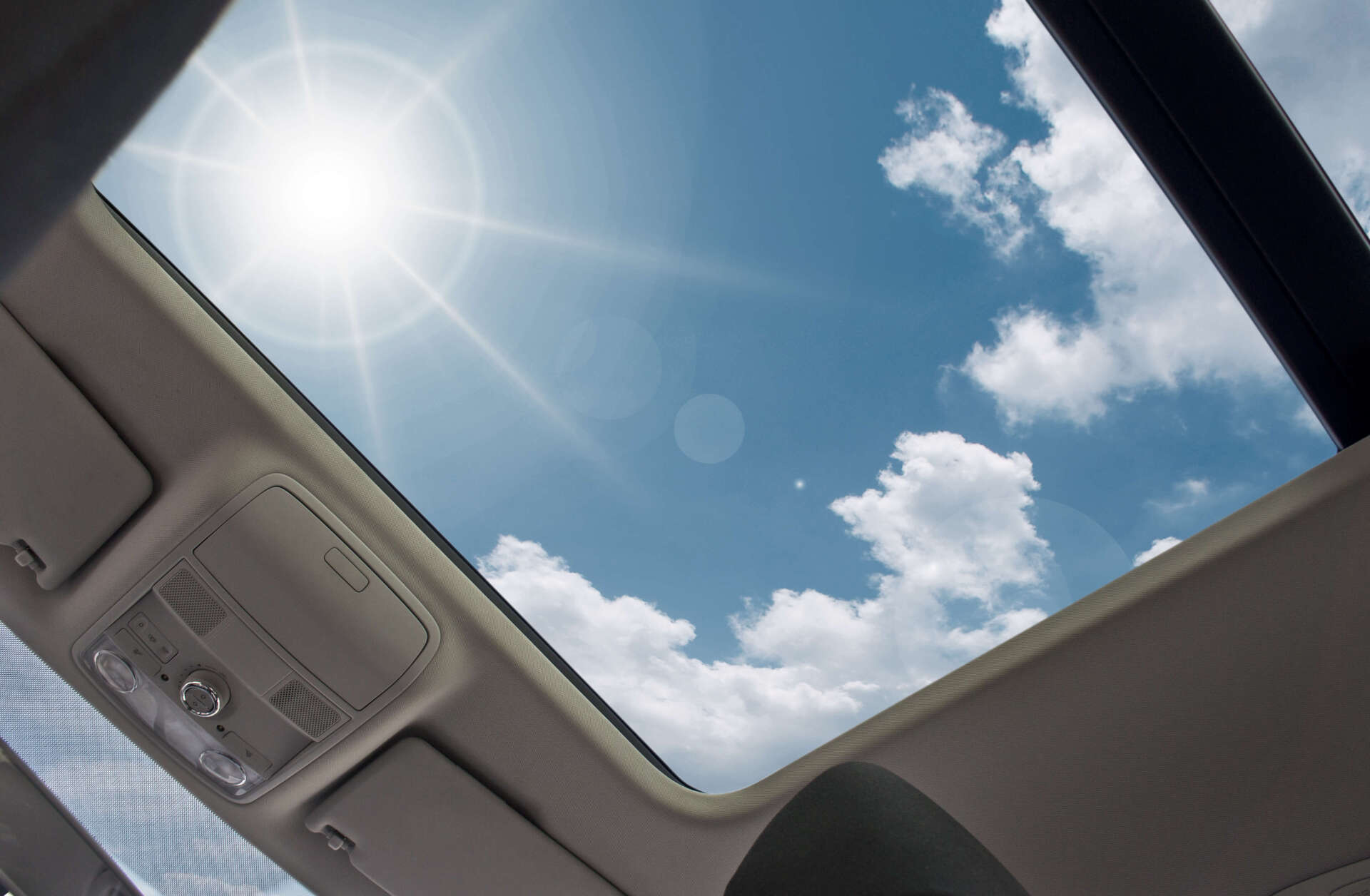
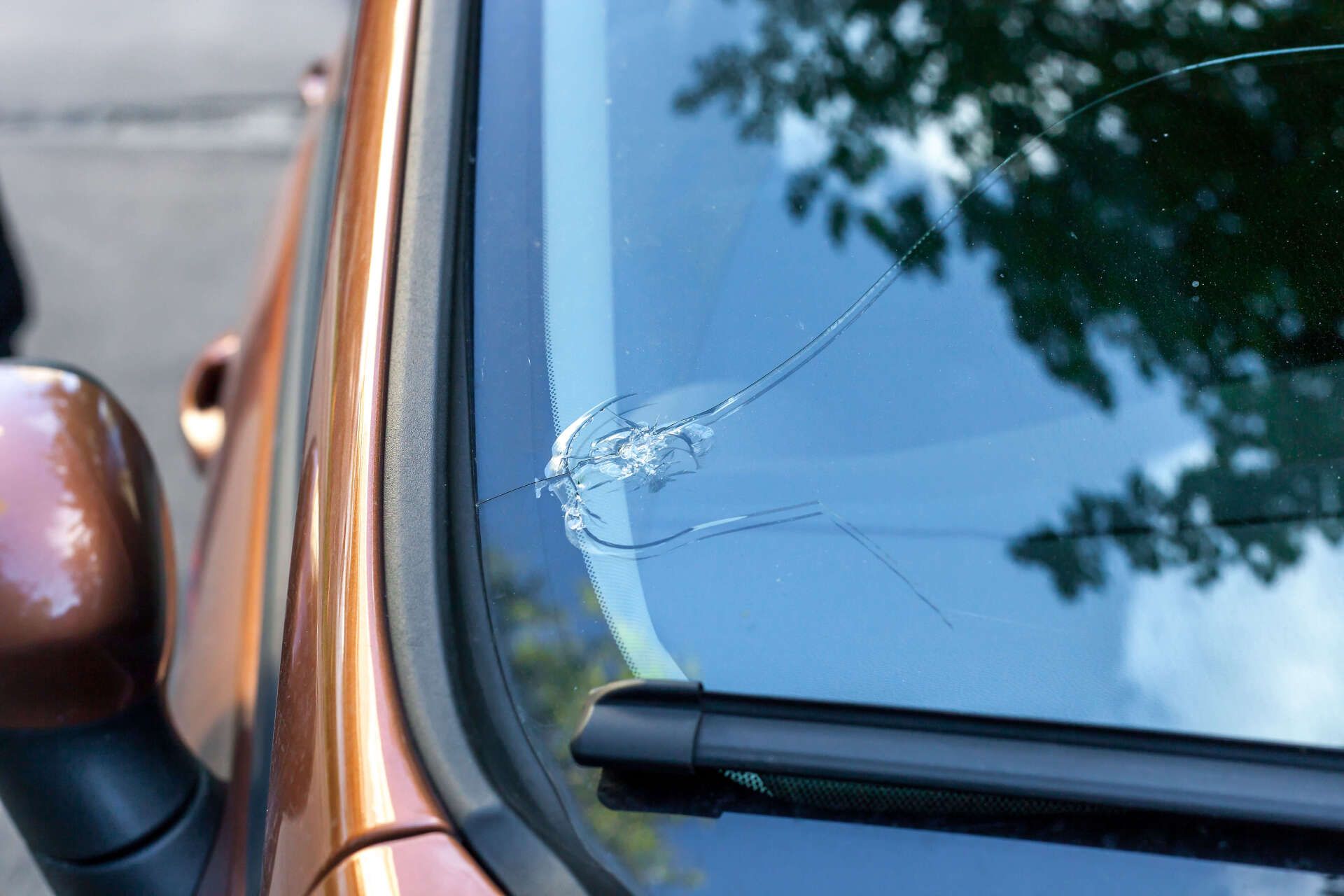
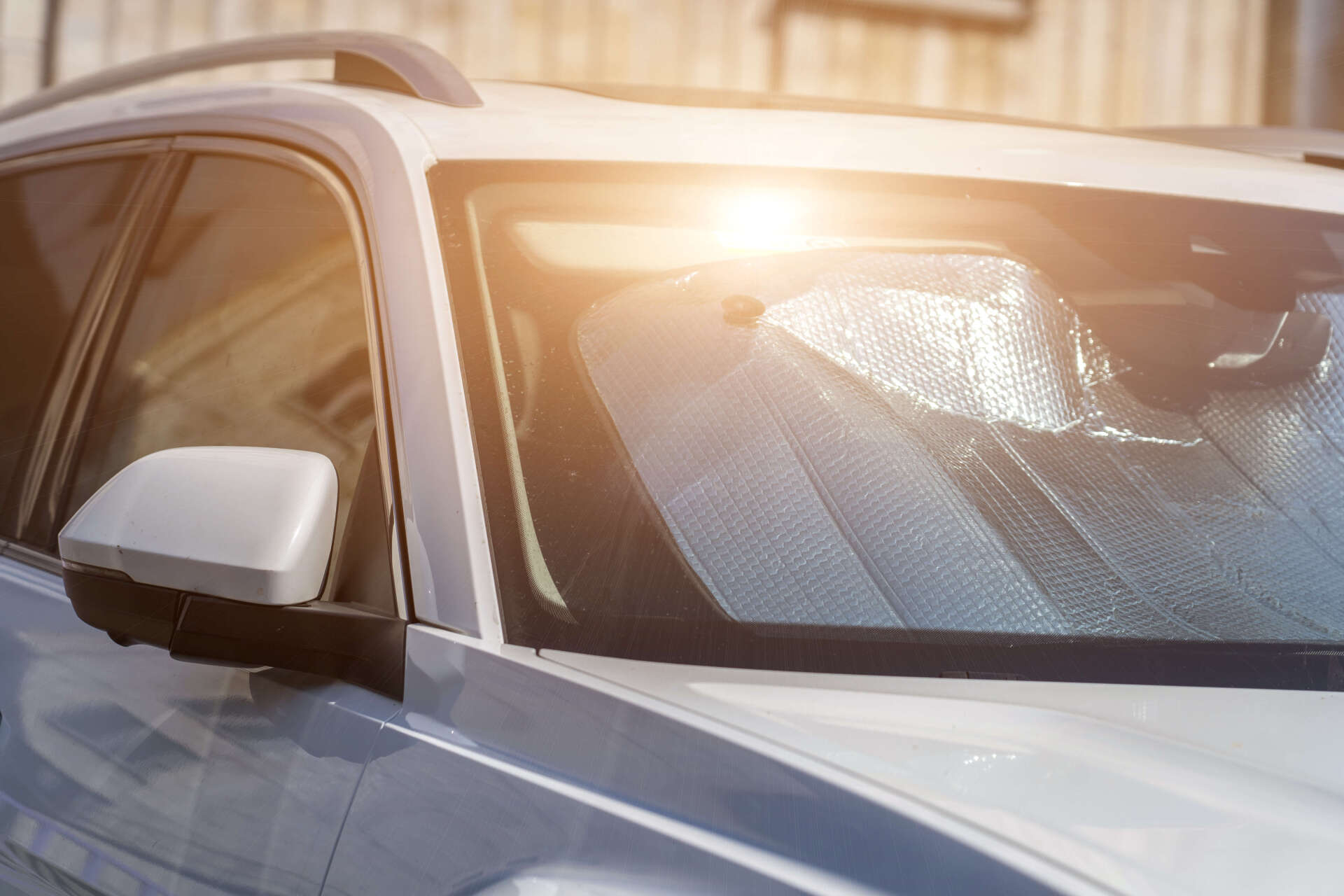
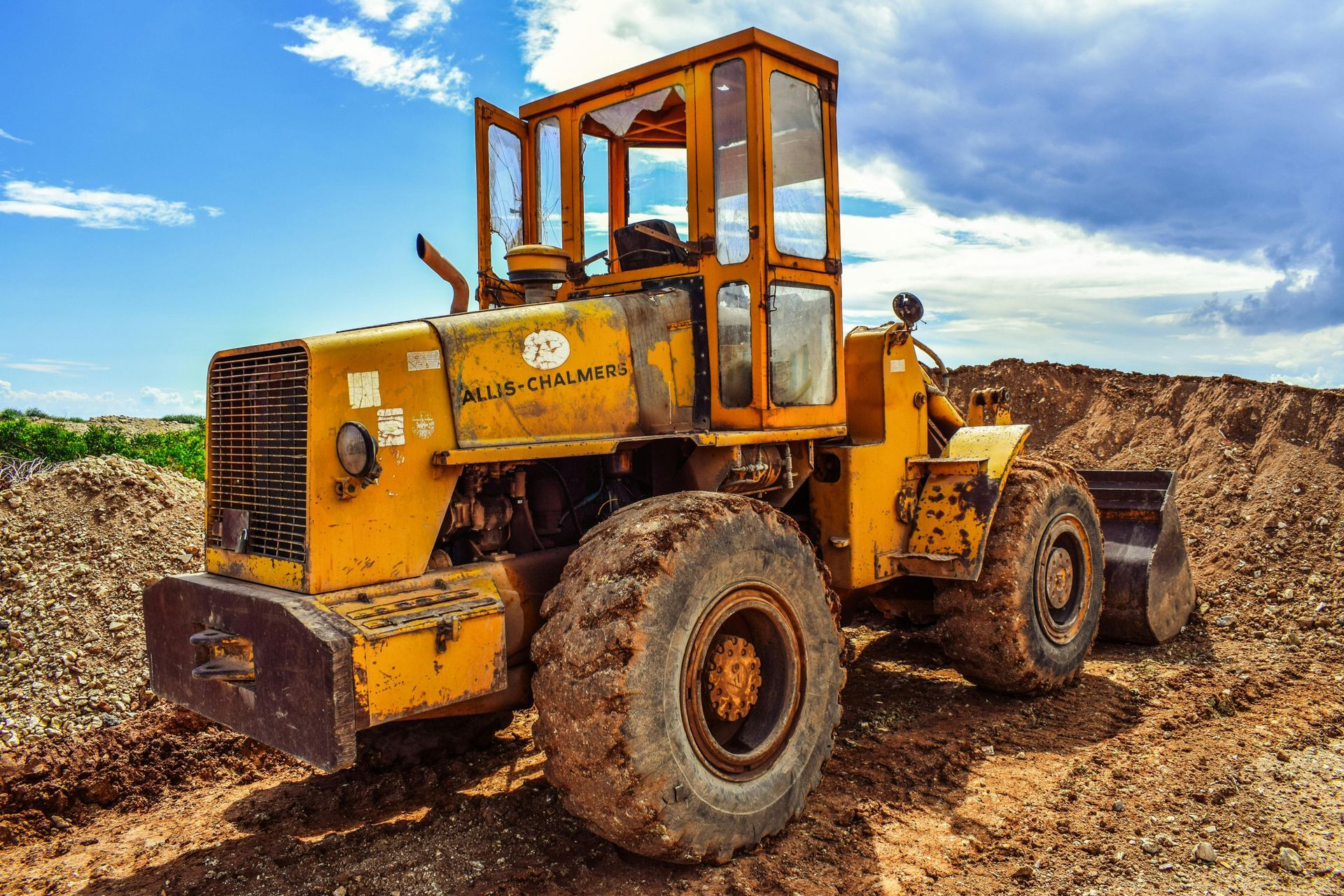
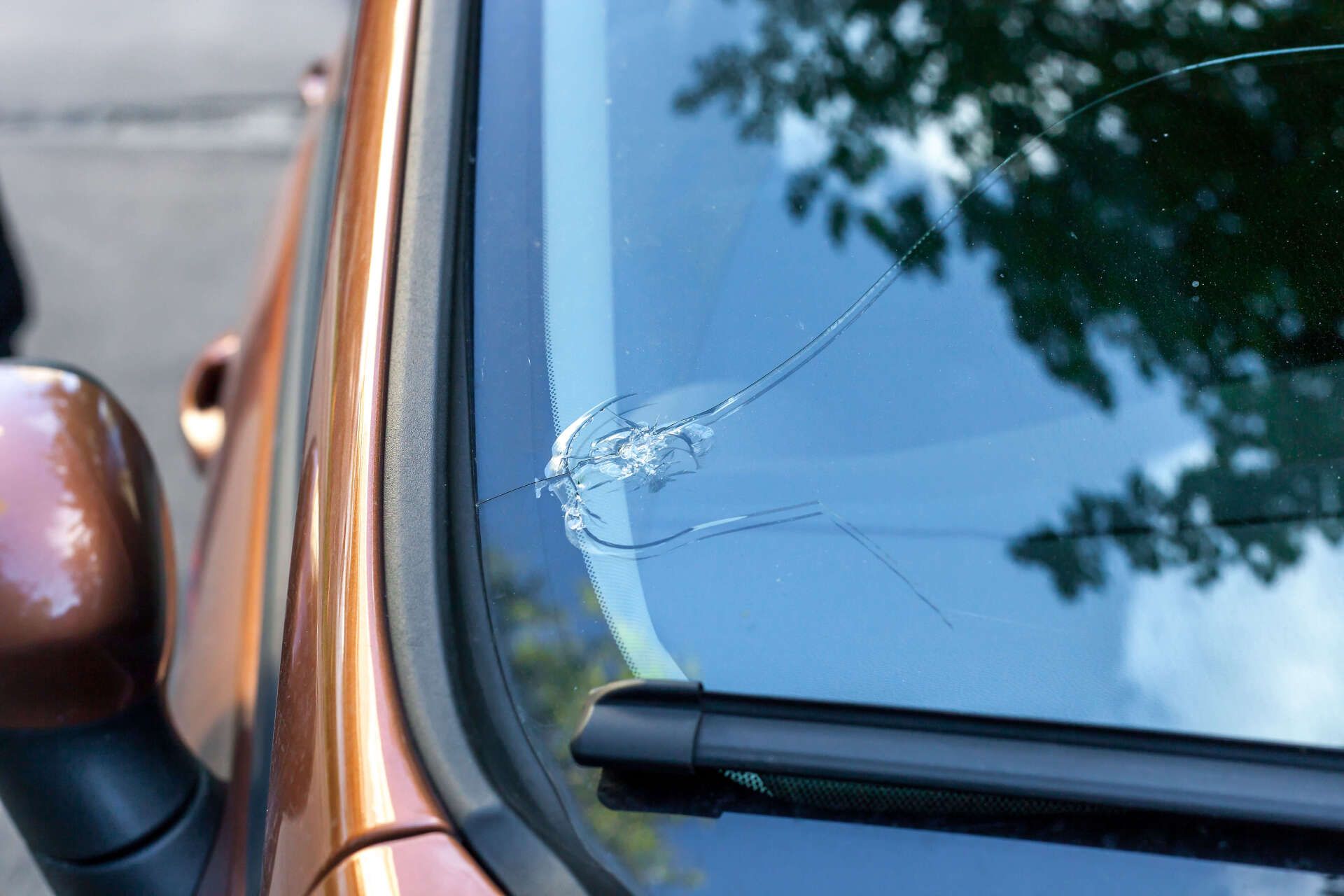
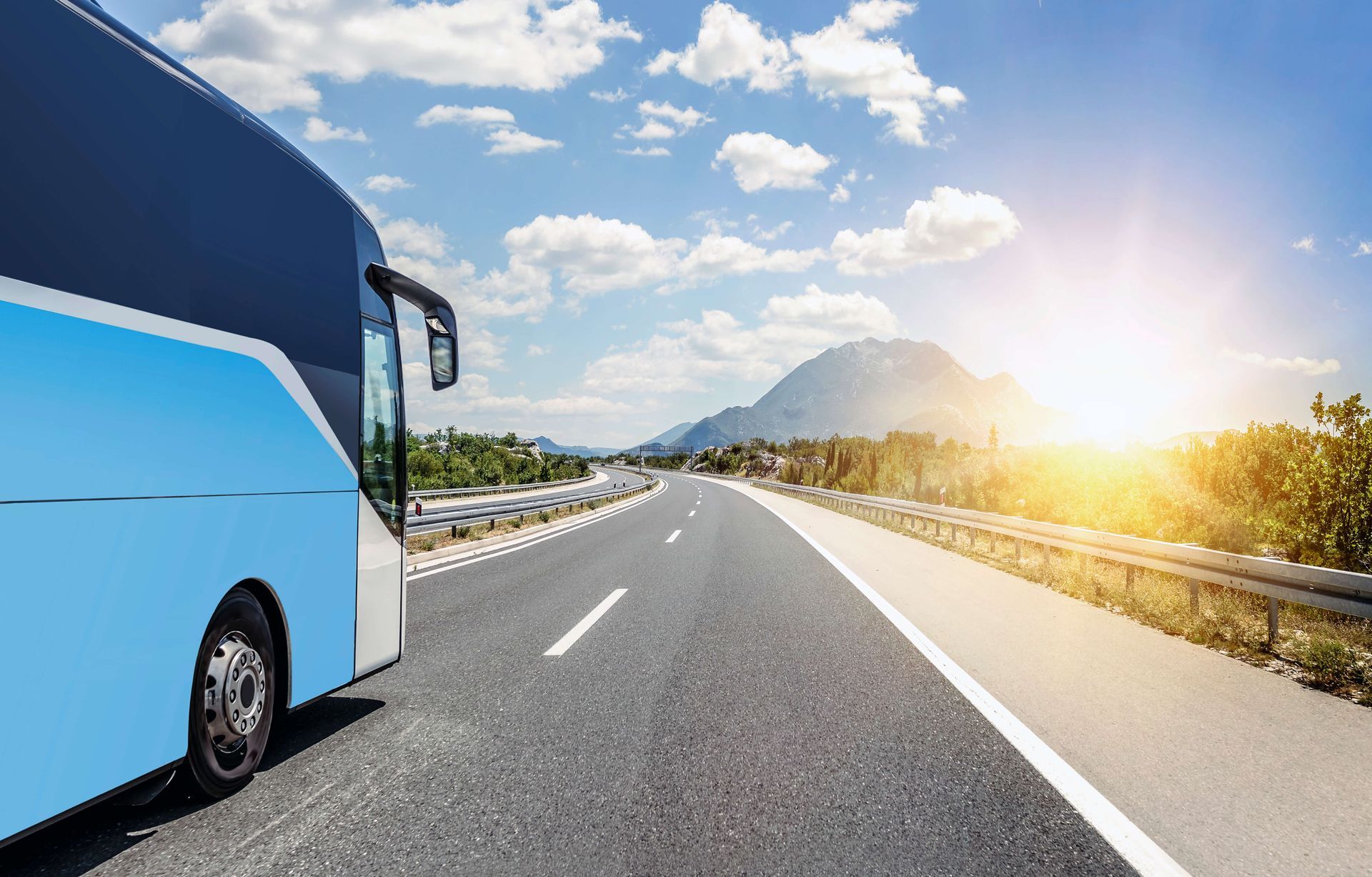
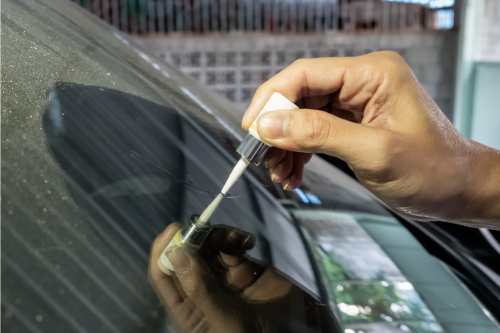
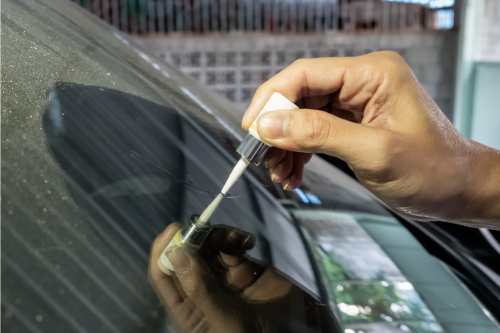